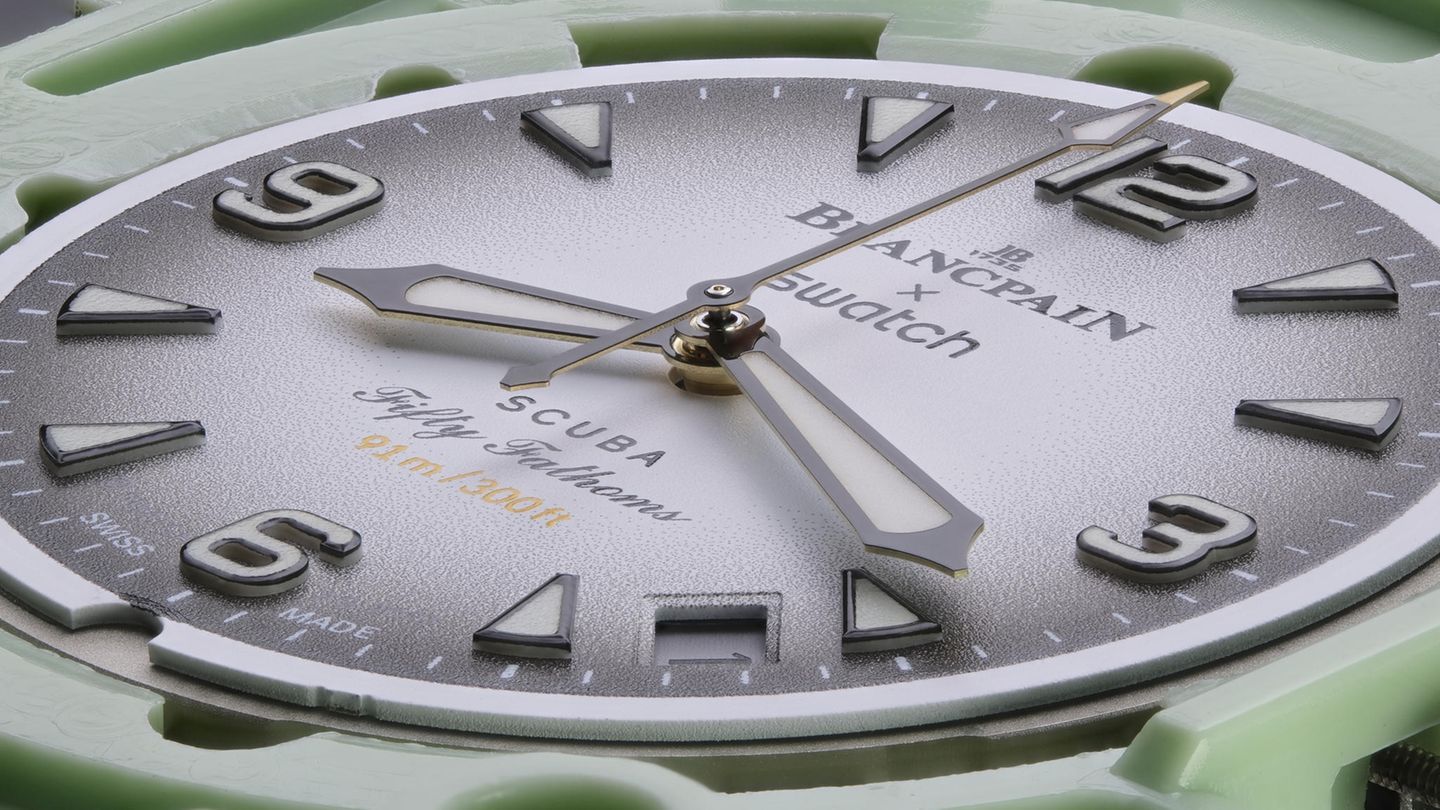
Eigentlich sollte das alte Gebäude der ETA, einem Schweizer Hersteller von Uhrwerken und Uhren mit Wurzeln bis ins Jahr 1793, schon leer sein. Doch hier in Bettlach brennt noch Licht. Denn seit der Swatch-Konzern, zu dem ETA gehört, die Moonswatch und die Blancpain-Kollaboration lanciert hat, stehen die Bänder keine Sekunde still. Mehr noch: Sie dürfen es nicht. Die Bedienung der enormen Nachfrage ist auch ohne Produktionsausfall kompliziert genug.
In Bettlach, einem von derzeit vier Standorten, an denen Swatch die beliebten Hype-Uhren herstellt, stehen die schweren Maschinen, mit denen die Gehäuse und zahlreichen Einzelteile für die Uhren im Spritzgussverfahren gefertigt werden. Außerdem hebt Swatch hier Bioceramic aus der Taufe, den neuartigen Rohstoff, der nicht ganz Plastik, nicht ganz Keramik, aber auf jeden Fall haltbar und schick ist.
Am Anfang einer Moonswatch steht eine Spaghetti
Im Keller beginnt die Geburt einer Moonswatch oder einer Blancpain Scuba. Hier entsteht das besagte Bioceramic. Das ist ein Werkstoff aus Keramikpulver, Farbpigmenten und biobasiertem Kunststoff, der aus Rizinusöl gewonnen wird. Es ist die Grundlage für beide Modelle. Aus langen Fäden, die man intern Spaghetti nennt, hackt sich die Maschine säckeweise Pellets zurecht.
Die richtige Mischung für diesen Rohstoff zu finden, verrät ETA-CEO Damiano Casafina dem stern bei einer Führung, war keineswegs leicht. Die Nächte waren lang, der Weg weit. Doch gleichzeitig war die Lust auf das vielversprechende Projekt so groß, dass man durchzog.
Durchziehen. Das heißt Maschinen einstellen, Gussformen besorgen, Material beschaffen, alles einstellen und unendlich viele Lösungen für ebensoviele Probleme finden. Und vor allem: absolute Geheimhaltung. Im Gespräch mit Nick Hayek, Swatch CEO und Mitglied der Konzernleitung der gesamten Unternehmensgruppe, sagte er dem stern, dass an der Moonswatch rund ein Jahr gearbeitet wurde, bevor die Weltöffentlichkeit davon erfuhr. Ein Erfolg, auf den ein Unternehmen im Internetzeitalter stolz sein kann.
Weiter in der Fertigung: Das Bioceramic wandert in Bettlach eine Etage höher. Hier stehen die großen Roboter und Pressen, welche die Einzelteile herstellen. Jedes noch so kleine Teil fällt bei Swatch vom Band. Eingekauft wird nichts, Fernost hilft nicht aus. Das ist auch der Grund dafür, warum man die erfolgreichen Modelle nicht parallel zur Nachfrage liefern kann. Der Aufbau der Maschinen, der Umzug in ein neues Werk – das alles dauert seine Zeit.
In Grenchen riecht es nach Farbe – viel davon
Nach ungefähr zehn Autominuten ist die Gruppe am zweiten Standort der Führung angekommen: Grenchen. Tatsächlich wirkt das Werk hier am Hauptsitz von ETA deutlich moderner. Es steht in direkter Nachbarschaft zu einer großen Wiese, im Hintergrund baut sich der Jura auf. Casafina deutet auf das Flachdach und erklärt, dass ihm dort eine Etage fehlt. Was in Bettlach steht, sollte eigentlich längst hier sein. Doch der Umzug muss sich der Produktion der Moonswatch und der Blancpain-Swatch unterordnen. Also dauert es.
Im Werk schmeißt man sich in Schale – denn hier darf kein Staub rein. Also Haube an, Schutzanzug an und ein paar Überzieher für die Schuhe. Dann geht es über Klebestreifen auf dem Boden, an denen bitte auch der letzte Krümel bleiben soll, in die heiligen Hallen. Es riecht stark nach Lack. Casafina erklärt, dass hier unter anderem die Zifferblätter entstehen. Es geht vorbei an zahllosen Maschinen, die tagein tagaus der gleichen Tätigkeit nachgehen: Rohling rein, Grafik drauf, Rohling raus. Weiter. Nach erstaunlich vielen Arbeitsschritten kommen dann fertige Zifferblätter raus.
Drucker reihen sich an Pressen, Pressen reihen sich an Arbeitsstationen mit Mitarbeitern. Es mag verwundern, aber auch in einer Uhr für 260 Euro, beziehungsweise 390 Euro, steckt erstaunlich viel Handarbeit. Das hat zwei Gründe, erklärt Casafina. Erstens erhalte man sich auf diese Weise das Wissen, was die Maschinen wirklich tun – denn würde man den gesamten Prozess automatisieren, laufe man irgendwann Gefahr, dass niemand mehr so richtig weiß, was die Roboter da eigentlich machen. Zweitens sind die Arbeitsstationen wesentlich flexibler.
Es geht vorbei an fleißigen Mitarbeiterinnen, die die Leuchtmasse, heute nennt man sie Superluminova, auf die drehbare Lünette der Taucheruhr auftragen. Erst die Füllung, dann in einem zweiten Schritt etwas weißer Lack, damit man die Zahlen auch im Hellen lesen kann.
Eine Hochzeit am Alpenrand
Die Teile, die an diesem Tag und während der Führung hergestellt worden sind, fahren anschließend nach Sion Richtung Alpen. Ein Teil der Führung ist es nicht – zu weit. In Sion werden die Uhren final zusammengesetzt – bei der sogenannten Hochzeit. Anschließend werden sie getestet und landen dann – nach einer erstaunlich kleinteiligen Reise und viel Arbeit – im Verkauf.
Einige Stationen der Reise dieser Uhren finden Sie in der Fotostrecke.
Transparenzhinweis: Diese Reise in die Schweiz erfolgte auf Einladung von Swatch.